Auditor's Perspective: ISO 13485 QMS Requirements
The Framework for a Successful Operation:
ISO 13485: Section 4, Quality Management System
In the meticulous world of medical device manufacturing, ensuring quality isn’t just a recommendation – it’s an absolute necessity. When it comes to maintaining ISO 13485 certification, critical elements within the standards can be neglected and eventually require corrective action. When left unchecked, small issues can pile into a mountain of workload – and well, we like to honor our weekends!
We’re diving into Section 4 of ISO 13485, highlighting points that tend to get overlooked in a Quality Management System. This is the backbone of your business and is essential to the certification, reputation, and ultimately, success of your business.
Section 4: Quality Management System
Your Quality Management System (QMS) serves as the framework for your business, designed to ensure consistency and standardization for meeting customer and regulatory expectations. In best practice, the QMS effectively eliminates process redundancies, performance gaps, and waste of resources. World class organizations have world class quality management systems, and it truly shows.
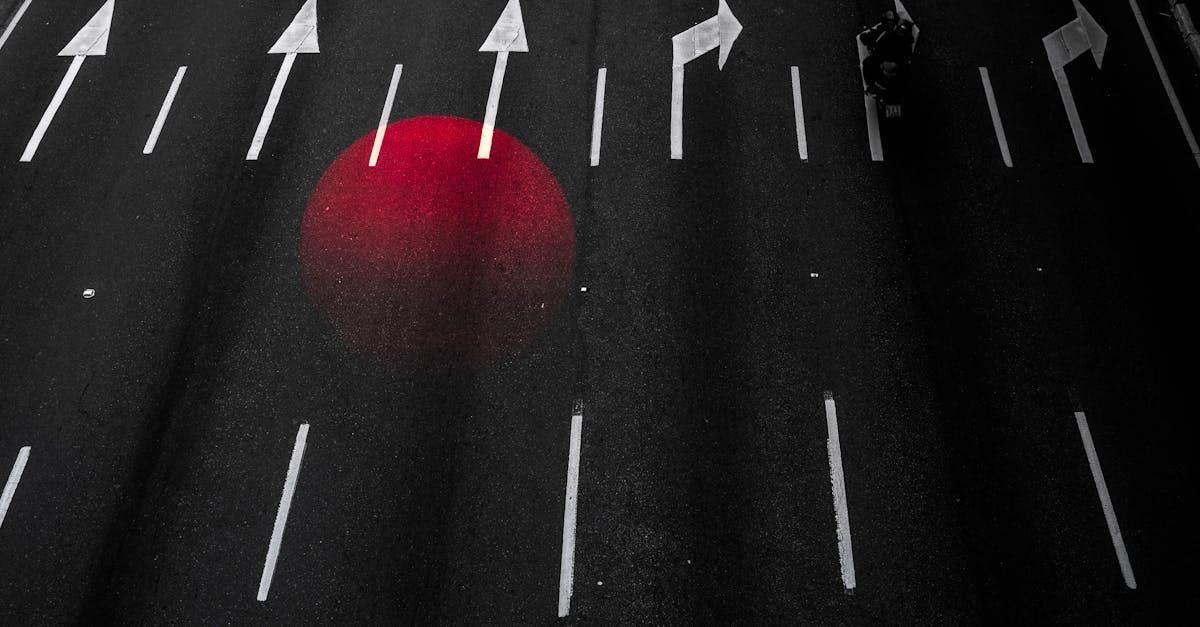
A well-designed QMS meets all of the following essential points:
Customer and Regulatory Requirements
A QMS ensures that your business process is effectively implemented to overcome any errors or obstacles that may hinder quality control standards and/or target deliveries. This allows your company to establish a reliable reputation, boosting customer satisfaction and loyalty.
Operational Efficiency
The QMS is the framework for building clear and consistent work instructions that ensure product requirements are met while minimizing process errors, bottlenecks, or redundancies. A well designed QMS should reduce resource waste, such as cost, time, or raw materials.
Continuous Improvement
An effective QMS allows you to create a structured approach to monitor and evaluate organization processes, methods, and practices. As such, you can identify necessary changes or areas of improvement and implement corrective/preventive actions to enhance your processes. The QMS empowers your business to continually optimize your workflow, decreasing waste and process variations.
Risk Mitigation
A QMS is crucial to the management of product quality, employee safety, and regulatory compliance. It serves as a roadmap that clearly establishes processes and contingencies intended to identify and prevent costly mistakes, reduce liability and customer dissatisfaction, and maintain adherence to regulatory requirements.
Below are notably common non-conformities in regard to ISO 13485 - Section 4:
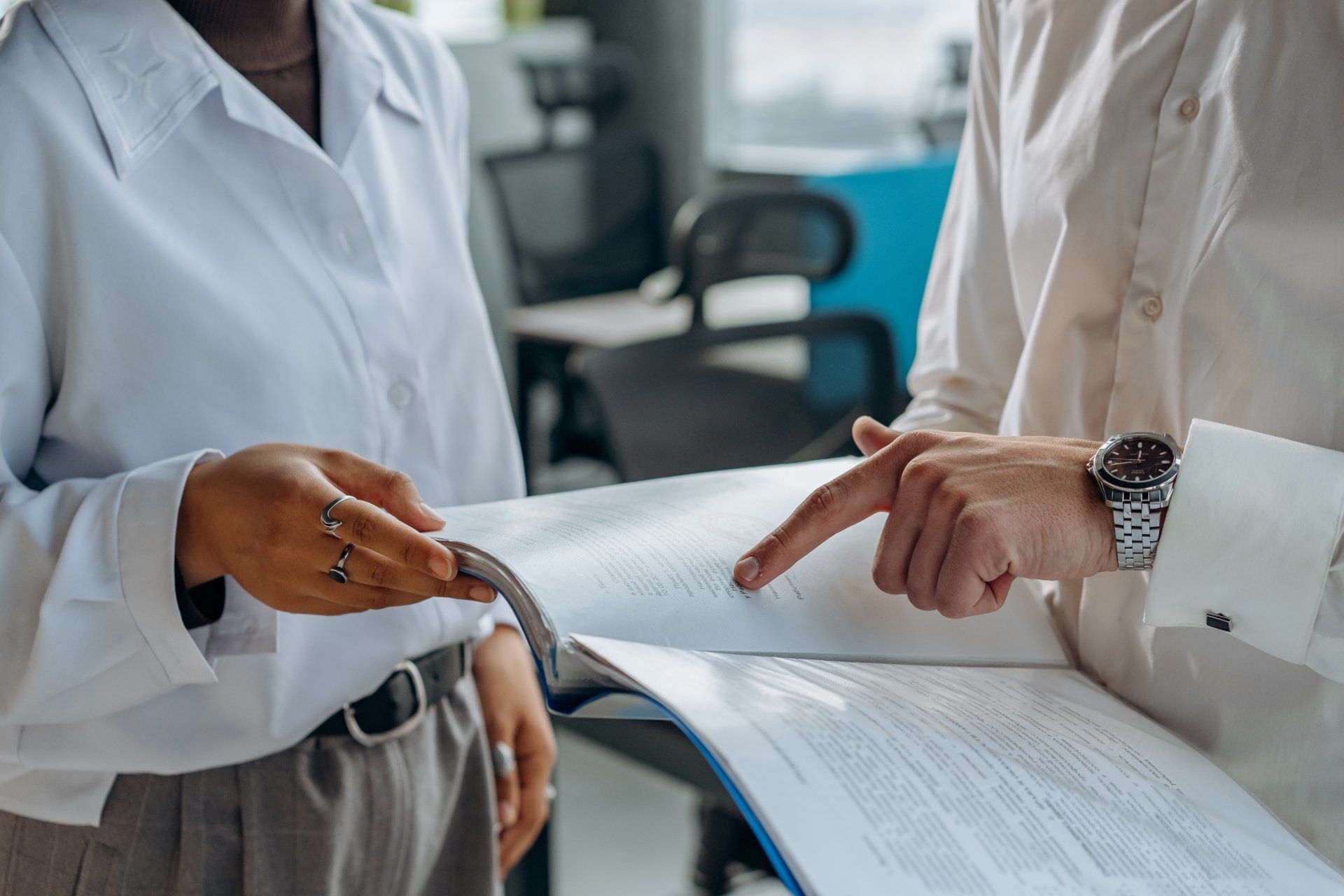
Section 4.1: Quality Management System - General Requirements
- Lack of application of risk management in all processes of the organization.
Calibration frequency, preventive maintenance frequency, and workforce training are often overlooked when it comes to risk management. However these are QMS processes that must be included in risk management such as FMEA (failure mode and effects analysis). Having a clear risk management system eliminates issues that could have been prevented with a proper plan in place. Don’t allow any room for error that can cause a possible recall. Trust us, those are a nightmare. - Poor process diagram not describing the inputs and outputs of the organization’s processes.
A good process diagram should effectively communicate the structure and sequence of an organization’s workflow and interdependencies. Put time into tailoring your process flow diagram to the critical and supportive processes of your organization. You want to make sure that every level of your process is included in your diagram. A process flow diagram that remains vague creates plenty of room for costly errors in the long run.
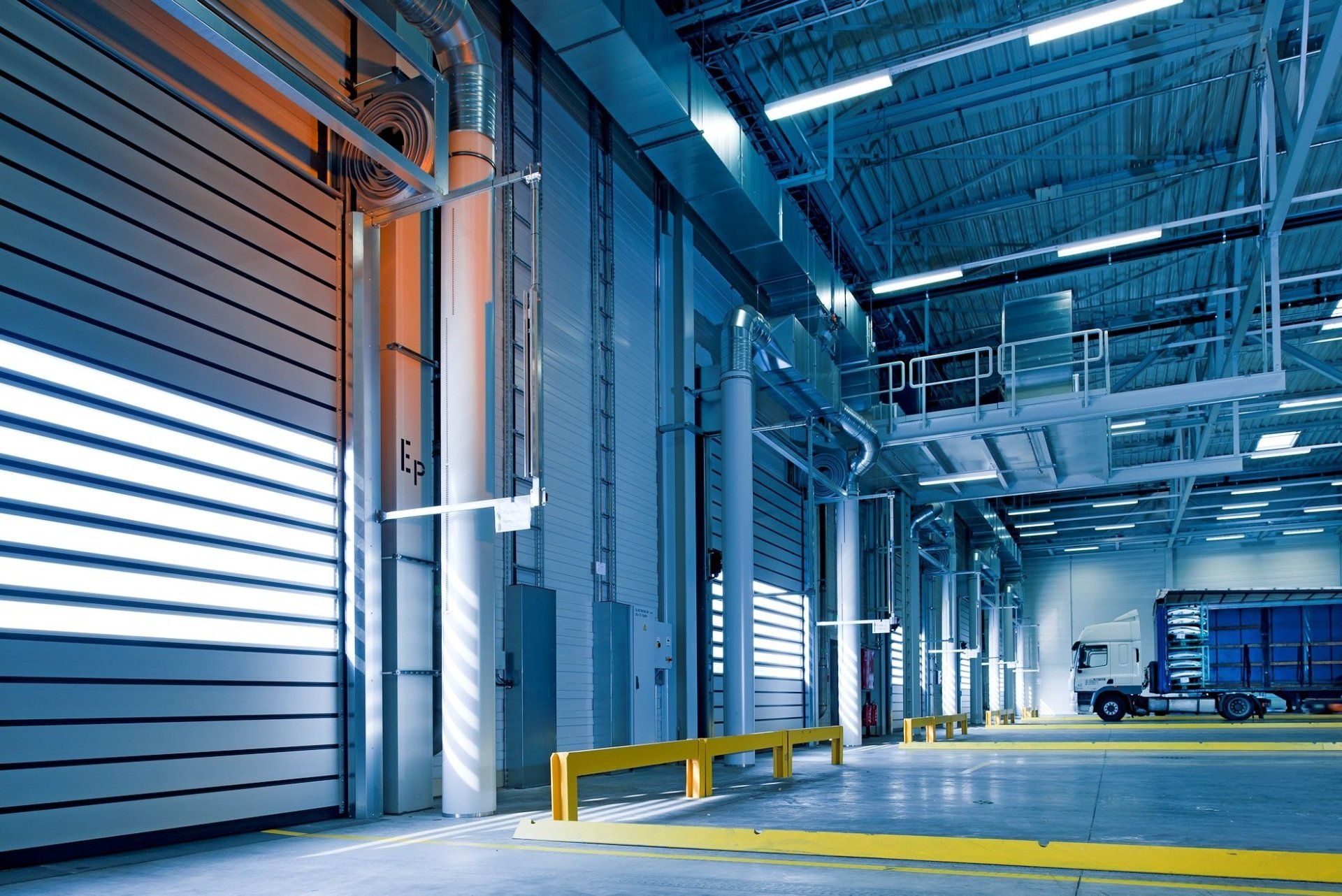
Section 4.2: Documentation Practices
- Poor justification for non-applicable processes as per ISO 13485.
If a clause in ISO 13485 does not pertain to your business structure, do not merely state that it is not applicable. Make sure you are clear in the justification as to why it is not applicable. A lack of explanation can be interpreted as poor understanding of ISO 13485. - No requirements for the review and update of controlled documents.
Make sure your control of documents clearly states the frequency of review and updates of procedures, work instructions and forms. It’s as simple as creating a schedule and a master list that can be tracked and updated as you implement new or revised QMS documents. - No controls for external documents such as equipment manuals and equipment diagrams.
Ensure that all external origin documents necessary to the operation and maintenance of equipment are also controlled. Create a system that lists each document for easy tracking and access. - No requirements established for the retention period of obsolete documents.
Old document revisions need to be retained within a timeline that is in accordance with regulatory requirements and risk-based factors. Create a trackable system outlining how obsolete documentation is to be stored, archived, and eventually disposed of. - No requirements established for the protections of confidential health information contained in records.
Research the data privacy regulations in your region. This could be HIPPA (US), GDPR (EU), or local equivalents. Create a comprehensive protection plan and train your employees on their responsibilities to sensitive data security for both internal and external inputs (such as a customer complaint that discloses confidential patient information). Accordingly, your QMS must include safeguards for confidential health information. - Evidence of poor corrections made to controlled records.
All versions of standard operating procedures and work instructions must include a comprehensive change record. Each revision should be numbered, dated, and signed (noting review and approval) with a justification and description of change. If handwritten, proper corrections should include a strikethrough of the corrected text accompanied with the correct information, date and initials for authorization. Don’t cut corners and overwrite typos. Unauthorized changes can appear as falsification of records. - Poor legibility in controlled records.
This one is pretty simple. Be sure that all information on your documents is clear and easy to read – especially hand-written details. Illegibility and clerical errors can cause confusion that may lead to a mistake. A misread number can lead to a span of issues from a minor inconvenience to a product failing compliance, or worse, a product recall.
Maintaining an effective QMS is not just beneficial to your operation, but a crucial prerequisite for sustainable business success. Whether you’re running a small business or a corporate powerhouse, active quality management ensures long-term viability and growth. Your high attention to detail will be rewarded tenfold in the long term with minimized margin of error and maximized efficacy.
Thinking about e-beam or X-ray sterilization for your products?
Contact Quantum EBX today
to learn how our expert consulting services can benefit your business!